Single Fluid Heating-Cooling System
Features
- No switching between jacket service fluids, preventing cross-contamination, corrosion or thermal shocks to the vessel.
- Process parameter deviations adversely affect product quality.
- Remote control panel with flameproof enclosures (suitable for gas group IIA, IIB)
- All wetted parts are in stainless steel. Condensate recovery is not feasible.
- Temperature range - 35°c to 250°c with precise temperature control, +/- 1°c.
- Totally enclosed skid & mounted on wheels for easy mobility. Rapid heating or cooling, reducing batch time.
- Automation - System is controlled by PLC system which can be integrated with SCADA
- User friendly plug and play features
- Consistent Batch time cycle resulting improved batch yield
- Rapid heating or cooling, reducing batch time.
How it Works?:
- This gives precise control over heating and cooling cycle. Thus, not only the temperature is controlled as a critical process parameter but also the heating-and-cooling time is controlled as a critical parameter. This results in batch-to-batch consistency and higher yield.
- Single fluid heating cooling system is normally connected to a single reactor, where the Temperature of the system is varied as per the process requirement, Thus maintaining the constant temperature difference between the process and fluid temperature
Solution:
- Single fluid heating cooling systems (SFHC) / Temperature Control Unit (TCU) are coming-up as an ideal solution to overcome most of the limitations with traditional multiutility based heat transfer and control system. where high accuracy and wide temperature ranges are critical for the development of new compounds and API’s.
SFHCS / TCU Usage:
- Repeatability and accurate recordable. Fully automatic capability, hence less manpower required.
- Programmable heating and cooling ramps for accurate unsupervised operations
- Rapid heating and chilling profiles can be designed, reducing batch times.
- No switching between jacket service fluids, preventing cross contamination, corrosion or thermal shocks
- to the vessel.
- Suitable for the very cold operating temperatures required by today’s new chemical formulae and
- reactions.
- Smooth, continuous temperature control, with no gaps because there is no fluid changeovers.
- Accurate temperature control to +/- 1°C without risk to your reactor.
- Measurement for meeting FDA requirements.
- Savings on expensive raw materials can be made because the yield is maximized without adding excess
- reactions.
- No interruption of process and no hot spots, resulting in higher product yields and quality. Off batches are
- minimized, if not eliminated
Advantages:
- Repeatability and accurate recordable. Fully automatic capability, hence less manpower required.
- Programmable heating and cooling ramps for accurate unsupervised operations
- Rapid heating and chilling profiles can be designed, reducing batch times.
- No switching between jacket service fluids, preventing cross contamination, corrosion or thermal shocks to the vessel.
- Suitable for the very cold operating temperatures required by today's new chemical formulae and reactions.
- Smooth, continuous temperature control, with no gaps because there is no fluid changeovers.
- Accurate temperature control to +/- 1°C without risk to your reactor.
- Measurement for meeting FDA requirements.
- Savings on expensive raw materials can be made because the yield is maximized without adding excess reactions.
- No interruption of process and no hot spots, resulting in higher product yields and quality. Off batches are minimized, if not eliminated.
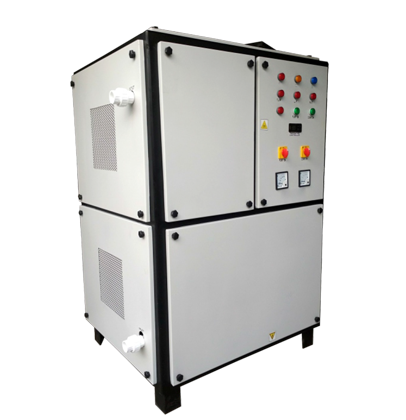